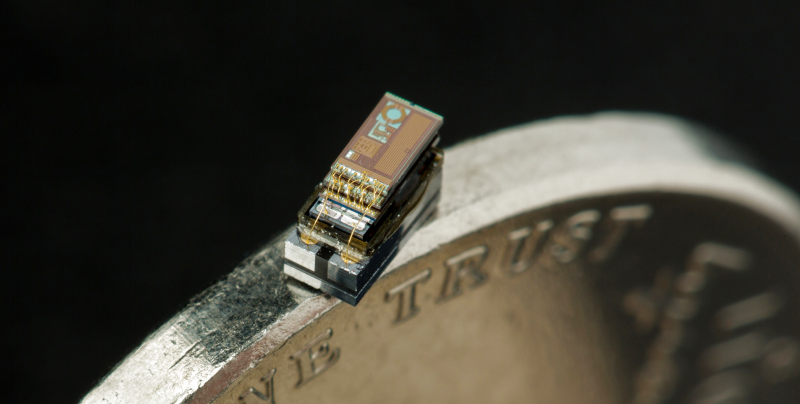
If you want to track a snail, you need a tiny instrumentation package. How do you create an entire data acquisition system, including sensors, memory, data processing and a power supply, small enough to fit onto a snail’s shell?
Throughout history, humans have upset many ecosystems around the world by introducing invasive species. Australia’s rabbits are a famous example, but perhaps less well-known are the Giant African land snails (Lissachatina fulica) that were introduced to South Pacific islands in the mid-20th century. Originally intended as a food source (escargot africain, anyone?), they quickly turned out to be horrible pests, devouring local plants and agricultural crops alike.
Not to be deterred, biologists introduced another snail, hoping to kill off the African ones: the Rosy Wolfsnail (Euglandina rosea), native to the Southeastern United States. This predatory snail did not show great interest in the African intruders however, and instead went on to decimate the indigenous snail population, driving dozens of local species into extinction.
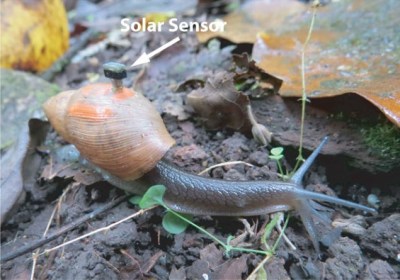
One that managed to survive the onslaught is a small white snail called Partula hyalina. Confined to the edges of the tropical forests of Tahiti, biologists hypothesized that it was able to avoid the predators by hiding in sunny places which were too bright for E. rosea. The milky-white shells of P. hyalina supposedly protected them from overheating by reflecting more sunlight than the wolf snails’ orange-brown ones.
This sounds reasonable, but biologists need proof. So a team from the University of Michigan set up an experiment to measure the amount of solar radiation experienced by both snail types. They attached tiny light sensors to the wolf snails’ shells and then released them again. The sensors measured the amount of sunlight seen by the animals and logged this information during a full day. The snails were then caught again and the data retrieved, and the results proved the original hypothesis.
So much for science, but exactly how did they pull this off?
The Michigan Micro Mote (M3)
The low-power circuit research team at the University of Michigan, led by David Blaauw, developed an ultra-miniaturized computer they dubbed the Michigan Micro Mote. The term “mote” refers to a wireless sensor node that can measure some quantity and report its findings to a larger computer system. Tiny motes like this are sometimes referred to as “smart dust”, a term that saw some hype in the early 2000s but thankfully hasn’t yet lived up to some of the more apocalyptic visions.
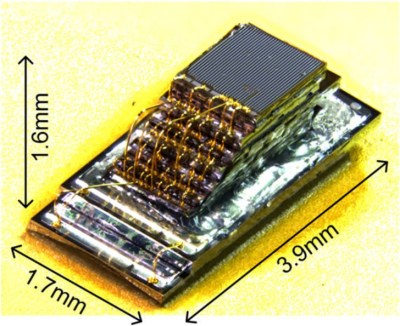
Not much larger than a grain of rice, the M3 has been dubbed the world’s smallest computer. Measuring about 2 mm x 2 mm x 3 mm, it consists of several bare chips stacked right on top of each other. Together they make up a complete wireless sensor node. Powered by a battery and a solar cell, they can measure something, store the results in RAM and send out the results using a wireless communication link.
The common thread linking the design of each of these elements is low power. And by low we mean really low: active power is in the microwatt or nanowatt level, while standby power is measured in picowatts. Such extremely low power consumption is needed because very little power can be generated and stored in the limited volume available.
Sensors
The top layer of the Mote is a sensor. The Micro Mote team has developed sensors for temperature and pressure as well as an image sensor. The temperature sensor is an ultra-low power one that can measure between zero and 100 °C, with an accuracy of about 1.5 °C, using only 71 nW. The pressure sensor is a MEMS device designed to measure the pressures inside the human body. Such a measurement can be useful in diagnosing glaucoma (when embedded in an eye) or tracking the efficacy of chemotherapy when inserted into a tumor.
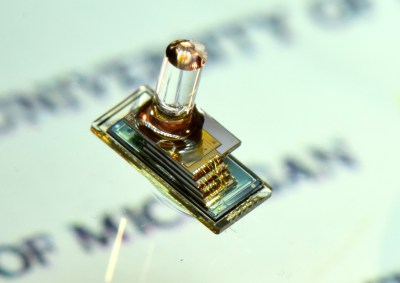
As for the image sensor, those looking for full-motion HD video will be disappointed: a monochrome sensor with 160 x 160 pixels is all that fits inside the volume and power constraints. A gradient index rod lens is fitted on top of the sensor to focus the image. The sensor can work in a low-power mode in which it performs motion detection by scanning a very low resolution image, only taking a full-resolution picture when there is significant movement.
The snail study actually used Micro Motes with a temperature sensor, and cleverly used the solar cell, described below, for both light sensing and power generation, eliminating the need for a power-hungry dedicated light sensor.
Data processing
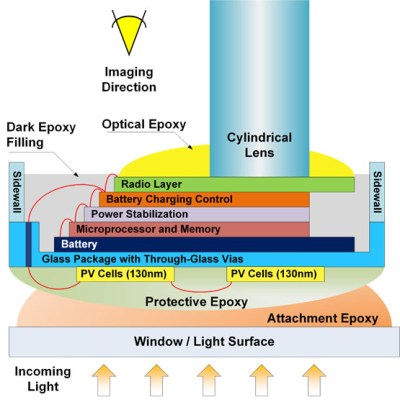
The heart of the Mote’s operations is formed by pair of microprocessors. Both are ARM Cortex-M0s, but each is made in a different manufacturing process to either provide high performance or extremely low power. The higher-speed CPU is needed for such tasks as processing the data from the image sensor, while the lower-power CPU does general housekeeping tasks such as coordinating data flow between the different chips.
The interface between the CPUs and the rest of the system naturally had to be ultra-low-power as well. Standard buses like SPI and I2C were far too power-hungry; the research team therefore developed a new bus named MBus. Geared towards integrated nanosystems, it is able to work with subsystems that are in sleep mode or completely powered down.
Communications
The Mote’s miniscule size means that there are no connectors available to get data in or out, so all communication has to be done wirelessly. Two interfaces are available for this: an optical path for system programming, and a radio link for outputting data.
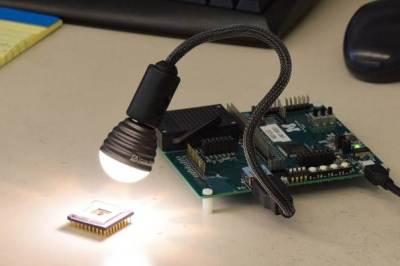
The optical path uses photodiodes that are strategically placed near the bond pads so they’re exposed to ambient light. By flashing light onto them in a specific pattern, the CPU enters programming mode, enabling the user to write into the main code memory.
The sensor data can be read out again using low-power radio: the user hold a receiver near the Mote to read out any data stored in its memory. Transmitting in the 915 MHz ISM band, the radio has a range of about two meters, although Dr. Blaauw says the plan is to increase that to 20 meters. This larger range would also allow multiple motes to communicate with one another, which would enable complete self-contained sensor networks. The limited power budget and physical constraints on the antenna make this a real challenge however.
Power
The Mighty Mote is powered by a lithium battery, again miniaturized to fit in the chip stack. Its capacity is a miniscule 5.7 uAh (for the image sensing version) or 2 uAh (for the other two versions). This is about one-millionth the size of the average smartphone battery, but still enables the Mote to work for a day or two. However, this can be extended indefinitely thanks to the solar cell that forms the bottom layer of the stack. This cell has an area of about one square millimeter and generates around 20 nW, depending on the amount of light.
A power management unit (PMU) generates the proper supply voltages (1.2 V and 0.6 V) for the various chips from the battery’s 3.8 V. Is also manages the operation of the solar cell, tracking its maximum power point to extract as much energy as possible. All chips also include generous amounts of on-chip decoupling capacitance, because the Mote is way too small to hook up even the tiniest of SMD capacitors.
In the Tahitian snail study, the control signals of the PMU were cleverly used for reading out the incident solar radiation. As the amount of light fluctuates, so does the frequency of the internal charge pump, and by logging this value the researchers obtained an accurate measurement of the solar radiation without having to add a separate light sensor.
Packaging
As mentioned above, a complete system is made from these parts by simply stacking the chips in a staircase-like fashion and wiring them up with gold bond wires, which is basically the same way ordinary multi-chip-modules (MCMs) are manufactured. The solar panel is at the bottom, with the sensors located at the top. The entire assembly is then encapsulated in epoxy, with transparent sections where needed.
The exact packaging design is dependent on the end application of the Mote. For the snail study, the chips were simply encapsulated in black epoxy with a window for the solar cell, then glued onto a bolt that could be threaded into a nut on the snail’s shell. Motes that will be implanted into eyes or tumors will need a bio-compatible enclosure, while those meant to work in harsher environments may need a stronger package.
Applications
Early in its development, the Micro Mote was aimed at medical applications such as measuring pressure inside eyes or tumors. A similar design was also developed that could be injected into the body. Not much has been published on medical applications of the Mote since about 2016, but we imagine that’s not for a lack of opportunities, since it should make development of things like smart pills much easier.
The Tahitian snail study is a great example of using wireless sensor nodes in conservation efforts. The research team is already working on another study involving monarch butterflies, which requires even more miniaturization to fit the devices to the monarchs’ tender bodies.
The version with the image sensor has potential applications in security and surveillance. A wireless, autonomous camera the size of a grain of rice can easily be hidden almost anywhere. However, the limited range of the radio still precludes actual remote observation.
A company called Cubeworks, a spinoff of David Blaauw’s research group, is commercializing the technology by making small wireless sensors for applications in logistics and pharmaceuticals, such as temperature logging of a chemical while it is being transported. This can help ensure that high-value goods like vaccines have been kept properly refrigerated throughout their entire journey from factory to clinic.
Overall, the Michigan Micro Mote is a great example of how to build electronic systems in an extremely confined space and with an even smaller power budget. While not exactly within reach of the average hobbyist, the basic ideas can be replicated in a larger volume using commercially available components. Snails might be a bit too small to work with, but I’m already thinking of all the sensors I could attach to my cat’s collar. Something more than just a camera, of course.
[Heading image: a Michigan Micro Mote sitting on the edge of a coin. Credit: Martin Vloet, University of Michigan]
No comments:
Post a Comment