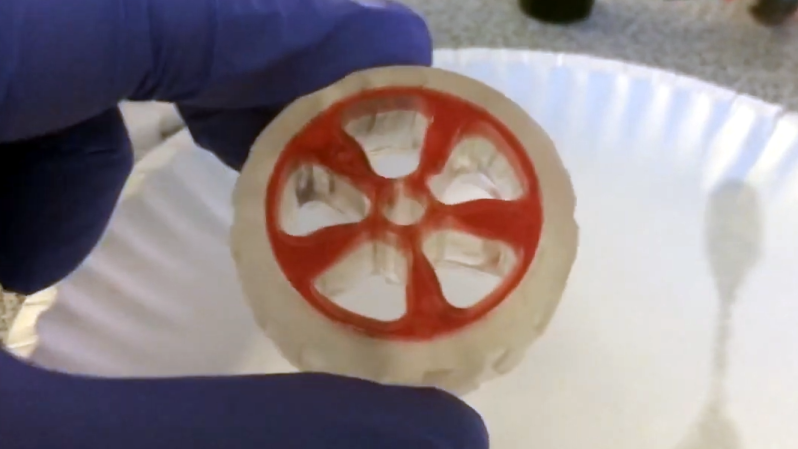
Resin printing is a fantastic way to create parts, but multi-material printing isn’t really a possibility with resin. That is, unless you use [Cameron Coward]’s method for creating multi-material resin prints.
[Cameron]’s idea relies on the fact that handling and curing UV resin can easily be done outside of the printer itself. First, one prints what we’ll call the primary object. This object has empty spaces representing the secondary object. Once the primary object is printed and finished, these voids are carefully filled with a different resin, then cured with UV light. The end result is a single multi-material object that is, effectively, made from two different resins.
[Cameron] demonstrates this concept wonderfully by printing a wheel in clear, flexible resin. This wheel has a void in it where the hub would go, but instead of printing a hub and gluing it in, the hub-shaped void is carefully filled with a different resin. Exposing that added resin to UV light cures it and bonds it to the flexible wheel. The result? A one-piece wheel with a squishy tire and a rigid hub.
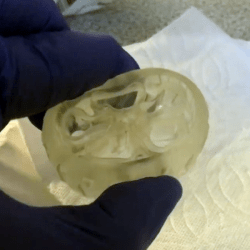
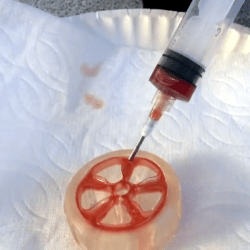
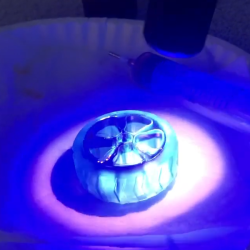
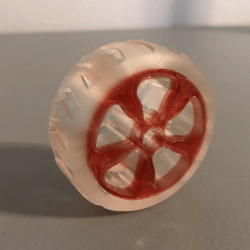
One shortcoming to this method is that UV has to be able to reach the added resin, so no filling of internal cavities where UV can’t shine directly on the liquid resin. Otherwise, it seems pretty flexible, and a good idea to keep in one’s mental toolbox. It’s also possible to work in stages, so complex shapes or large volumes don’t need to be done all at once.
There’s a short video embedded below that shows the whole process. Really helping this idea along is the fact that resin choices and properties are considerably wider and more varied than they were even just a few years ago, so whatever your needs, there’s probably a resin out there for it.
No comments:
Post a Comment